What is Conformal Coating?
In electronics manufacturing, conformal coating is used to protect sensitive printed circuit boards (PCBs) and components from exposure to environmental conditions such as moisture or temperature. It also protects from other contaminating factors such as solvents, chemicals, corrosion, mold and dust.
It’s very important that the coating completely covers the sensitive components of a PCB in order to provide a protective barrier. IPC-A-610, Acceptability of Electronics Assemblies is an industry standard for inspection in the electronics industry. It states conformal coating should be transparent, with uniform color and consistency and cover the PCB and components uniformly.
Inspecting Conformal Coating
As conformal coating is colorless, using white light illumination for inspection would be very difficult. A UV dye with fluorescing agents is added to the clear coating which “light up” (fluoresce) with a blue glow under a UV light source.
This blue glow allows for inspection confirming complete and intact conformal coating coverage of all areas requiring protection. Inspection criteria may include:
- Dark areas where a blue glow isn’t present indicating a lack of coating coverage.
- Circles with a glowing outer ring and dark center are typical of trapped air bubbles or pockets.
- Holes where the coating hasn’t fully covered will appear dark without any glow.
Types of UV Light
UV light is a spectrum comprised of 3 wavelengths which are known as UV-A, UV-B & UV-C. Conformal coating inspection is performed using only UV-A (long wave) UV with a wavelength of 320-400nm.
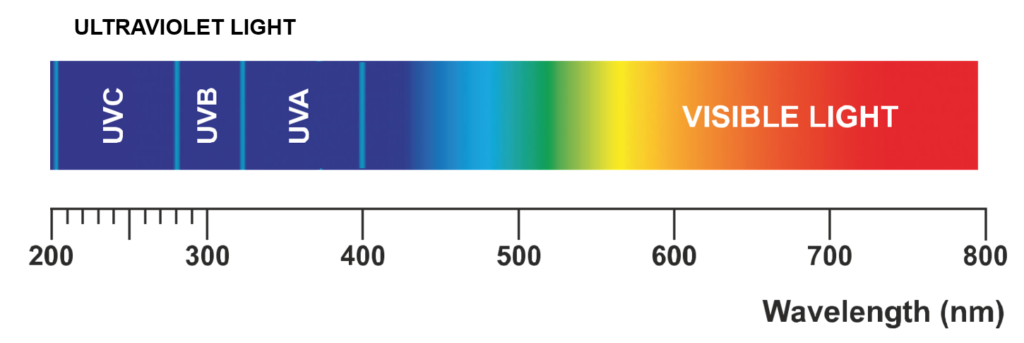
Best Practices for Using UV Light
UV light emitting in the UV-A wavelength is considered safe for use for inspection. Despite their safety, UV-A lights should never be operated without the use of UV-protective safety glasses and minimization of skin exposure to UV-A light. This can include long sleeve garment requirements and gloves.
In conjunction with a microscope, UV light works best when the ring light is positioned 6-8 inches from the sample. This also provides sufficient space for tools and soldering irons where applicable. Darker areas are preferred as white light can limit the effects of UV light fluorescence.
Ring lights attach to the microscope nosepiece and help keep the bench surface clear. They deliver bright, even illumination to the sample revealing greater details and ease in identifying defects. LED ring lights may include double or even triple concentric rings of LEDs, dimming and quadrant controls. LEDs that emit UV-A light are now incorporated into ring lights for inspection of conformal coating. The advantage of the smaller size of LEDs allows for ring lights which include LED rings of UV-A and white LEDs thus affording inspection using either. In conjunction with dimming and quadrant controls, a combination UV/white light LED ring light is a powerful tool for inspecting electronic components.
UNITRON’s Best in Class LED580 UV/Daylight Quadrant Ring Illuminator
The LED580 UV/Daylight Quadrant Ring Illuminator (P/N 15859-B) combines the best of both light sources. By producing both white and UV light, it allows the operator to inspect the sample for defects with white light, and then to perform higher magnification inspection of the conformal coating with UV light further ensuring complete, intact coverage and the absence of air bubbles or voids created during the coating process. For the user's safety, we also include a pair of UV-protective safety glasses.
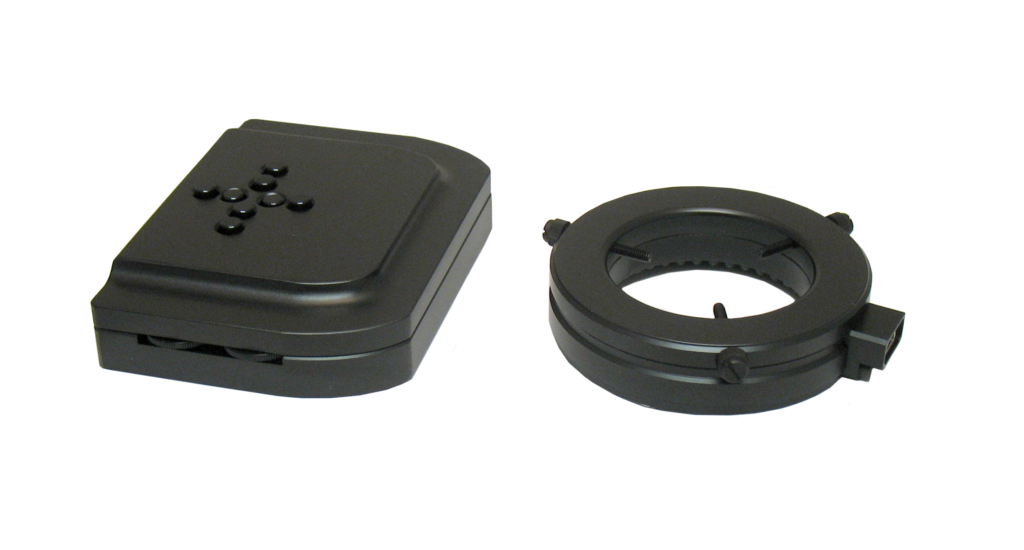
For questions about the LED580 UV/Daylight Quadrant Ring Illuminator or other illuminators for LX Microscopes by UNITRON, contact us at info@unitronusa.com.